How Fiber Optic Cable is Made
Oct 12, 2021 | Home Technology
While it may seem like magic or science fiction, fiber optic technology is very scientific and has been around for over half a century. But how does it work? How does glass become fiber optics? How can light transmit through a cable and reach its destination? (Hint: It’s not pixie dust and elves.)
In 1970, the engineers at Corning Incorporation’s research laboratory in Corning, NY stumbled upon a formula for making strands of glass that could transmit pulses of light containing data that could then be read by computers. Up until then, data could only travel over copper wires. Building upon this discovery, they tested fiber data transmission over longer distances, all with minimal signal loss. This new “low loss” fiber, as it became known, started the data and telecommunications technology revolution that continues over half a century later. But how is this glass fiber made?
The 3 Cs of Fiber
To understand why fiber is made the way it’s made, it’s important to first understand how light travels. Light waves travel in a straight line until they hit an object that reflects, refracts, or absorbs them. Fiber optics are designed to minimize reflection while maximizing refraction and eliminating absorption. The challenge with fiber optics was keeping the light signal inside the fiber all the way from beginning to end. This need to keep the signal inside the fiber dictated the materials and process by which liquid glass becomes usable fiber optic cable.
There are three major components in every strand of fiber optics: core, cladding, and coating.
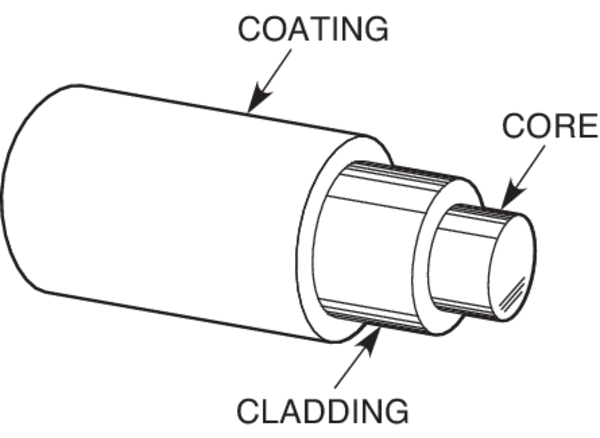
Contrary to popular belief, the core, where the light travels, is not hollow. Instead, it is solid, ultra-pure silica glass – so pure its contaminant levels are measured in parts per billion. This level of purity is essential for the light signal to travel down the fiber strand without degrading the light quality, which would degrade the data. Any time light hits an object, it loses a bit of strength. The key to success in fiber optic signal transmission is to minimize that loss by using ultra-clear glass. The clearer the glass, the better the light signal from end to end.
A second, less pure layer of glass called the cladding surrounds the entire length of the fiber core. This layer acts as a reflector to keep the light inside the core as it travels to its destination. Without the cladding, the light would escape the core and be lost. With the cladding, however, the light travels to its destination with minimal signal loss, preserving the integrity of the data from beginning to end.
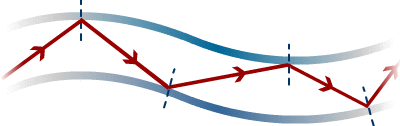
The third and final component is the thin rubber coating that protects the fiber from scratches and makes it easier for installers and technicians to organize the fibers. Usually, the coating is color-coded to make connection and installation easier.
Let’s look at the step-by-step process that starts with raw chemicals and turns them into the finished fiber.
Laydown & Consolidation
Making fiber starts by hanging a ceramic bait rod designed to attract silicon dioxide, a highly pure form of silica, inside an ultra-clean, climate-controlled container. The silicon dioxide clings to the ceramic rod and forms a thick cylinder of glass called a pre-form. The consolidation process then removes any moisture from the newly created pre-form in a high-temperature furnace and transforms the roughed-in silicon dioxide into a smooth, non-porous glass before sintering/melting the ends to shape it and ready it for the next step. This process results in the optical fiber blank that will become the strand in the third step.

Draw
The final step in creating the glass part of the fiber optic cable is the draw, which starts with the newly formed blank hanging vertically inside an ultra-hot furnace, heating the glass to the melting point. The tip of the blank heats up, softens, and begins to slowly drop, forming a very thin strand of glass on its way down, so thin it is measured in microns. This strand becomes the core and cladding. Depending on the size, each blank can produce up to 5 kilometers of fiber.
Coating
After the glass fiber has cooled, it is coiled onto large spools and shipped to a finishing factory where it is unspooled and sent through a machine that applies a thin layer of rubber to the outside of the strand. Coating the strand does not significantly add to the overall strength. The glass is strong enough on its own. Instead, the coating prevents the fiber from getting scratched and makes it easier for installers to handle and find where fibers connect, similar to the way copper wires are color-coded for easy organization.
Cabling

Even though individual fiber optics strands can carry a large amount of data by themselves, typically fiber optics are bundled into cables for ease of installation and to protect them from the elements. Often the individual fibers are bonded into 12-, 24-, 48-, 72-, and 96-strand colored ribbons that are then housed inside a protective rubber or metal conduit for deployment in a neighborhood.
Once they reach the home or business, the fibers are separated again into individual strands to serve customers. This allows many customers to get service from a single cable bundle in the ground without any of them sharing bandwidth with their neighbors because each household gets its own dedicated fiber.
Barring damage from an outside source, fiber optic cable should last for generations of internet users, with virtually unlimited bandwidth and speed.
- Fiber internet
- fiber optic cable
- how fiber optics are made